
For example, some resins are “stickier” than others and require more force to release from the mold. Your choice of resin may affect pin size or placement.
#Ejector pin marks how to#
It’s important to consider how to remove the part from your mold when you’re designing it, and ejector pin placement is a crucial part of how the part comes out of the mold. Factors to Consider When Designing Your Mold Ejector Blocksĭesigned for use on the surface of products with high warpage and to reduce ejector pin marks, ejector blocks have a lubricating hollow groove and are applied to the surface of thin products with a high surface finish. They hold the heads of the pins to prevent them from coming out during the injection molding process. Ejector PlatesĮjector plates work alongside ejector pins. The holes in the sleeves protect and guide the pin. Ejector SleevesĮjector sleeves are hollow ejector pins that have a hard-surface sleeve pin with a hole and a core pin that fits in the hole. Here are some other types of ejectors you may come across.
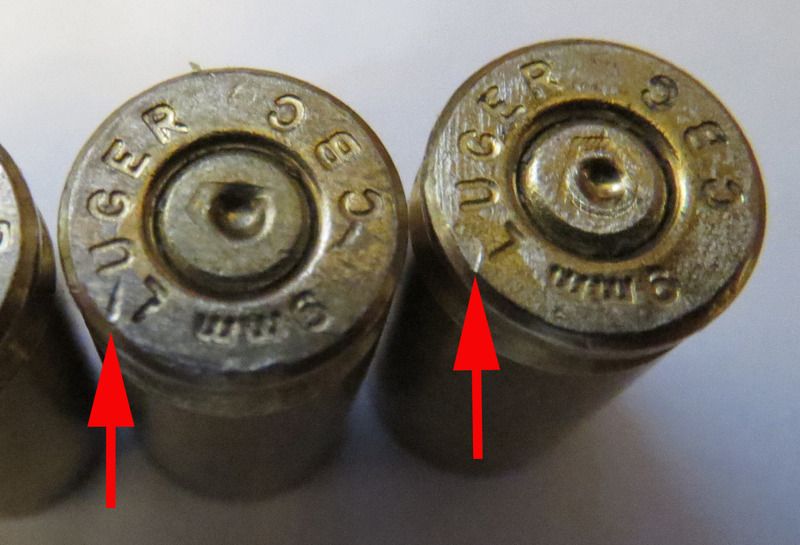
In some cases, ejector pins simply can’t do what you need them to. While these ejector pins work well in most temperatures, they are more expensive than other pin types. These pins have a special black surface coating that helps them withstand the high temperatures and provide additional self-lubrication to the pin, which is perfect for automotive applications. Since nitride H13 pins don’t work well in temperatures above 600° C, black ejector pins were developed to withstand working temperatures up to 1000° C. Nitride H13 Pinsīest for die casting, nitride H13 pins have a surface hardness level of HRC 65 to 70, which allows them to survive longer in working temperatures up to 600° C. Through hard pins last longest in temperatures below 200° C, so you’ll need a different pin type if you require higher temperatures. Mostly suitable for plastic injection molds, through hard pins have the same hardness throughout the ejector pin’s diameter. Using the wrong type of pin could result in extra expenses, either due to the pins having a shorter life and needing to be replaced more frequently or due to using a more expensive pin than necessary. While each type is excellent, they have their own characteristics and are designed for different environments. There are three common types of ejector pins. In order to minimize marks and maximize the effectiveness of the ejector pins, there are things you need to know and incorporate into your mold design. After the mold opens, the pins extend into the cavity of the mold, push the part out, then retract so the mold can close and be refilled. They are located in the B-side of the mold, which is where the part stays once the mold opens. What Are Ejector Pins?Įjector pins push a part out of the mold once it has cooled, occasionally leaving marks in the process. Let’s talk about ejector pins and what you need to know to incorporate them into your mold design.
#Ejector pin marks free#
If you’re currently designing a mold, have you taken into account the ejector pins that will help remove your part from the mold? Using the wrong type of pins or using them in the wrong location can prevent your part from being ejected in one piece that’s free of defects.
